Are you looking to add some light and color to your home? Soldering LED strips could be the perfect solution for you! It’s an inexpensive way of creating a unique lighting display that adds style and atmosphere to any space. Whether it’s used on your bedroom countertop, living room wall, or kitchen cabinets, LED strips provide beautiful accents of vibrant colors.
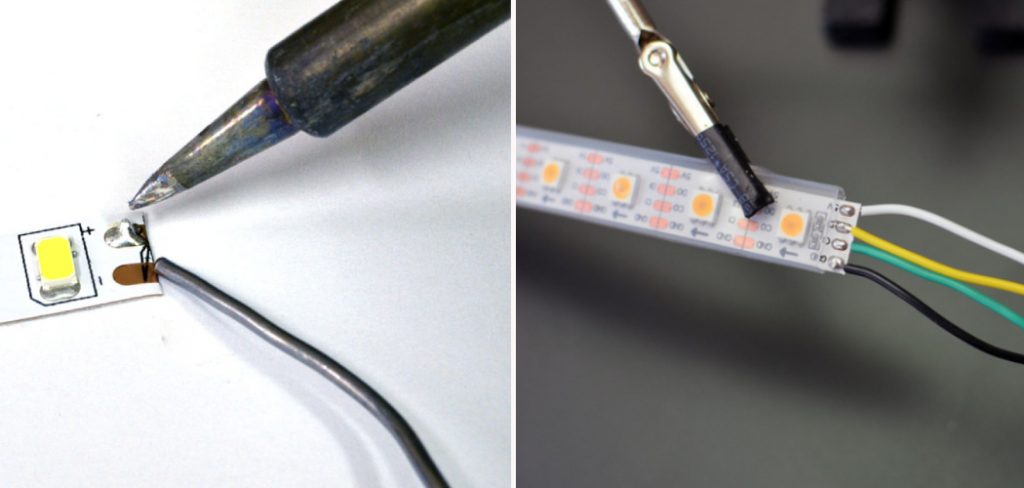
In this blog post, we will discuss how to solder led light strips by yourself – from gathering the tools you need to complete a successful project. Get ready to brighten up your favorite spaces with homemade LED DIY projects!
Can Led Light Strips Be Soldered?
Yes, LED light strips can be soldered! Soldering is a great way to make sure that your LED lights are securely and reliably connected. The process involves connecting two pieces of metal together by melting a bit of solder, which is a metallic alloy made up of lead and tin.
When soldering LED light strips, it is important to use the right type of solder for the job. Lead-free solder is best for soldering LED light strips. It produces a stronger, more durable connection and has a lower melting point than traditional lead-based solder.
It is also important to make sure that you have all the necessary tools before beginning the soldering process. You will need a soldering iron, rosin core solder, wire stripper/cutter, flux, and heat shrink tubing or electrical tape. Additionally, it is helpful to wear safety glasses when working with heat and electricity in order to protect your eyes.
Once you have gathered all of your supplies and put on your safety glasses, you can begin soldering your LED light strip. Make sure that the power is off before beginning, and use a wire stripper/cutter to strip any necessary wires. Apply flux to clean off the metal parts before soldering them together. Then, heat up the solder with a soldering iron and apply it to the joint of the two metals. When the solder is applied, use heat shrink tubing or electrical tape to insulate the connection and make sure it is safe from water damage.
Once you have finished soldering your LED light strip, you should test it before plugging it in for power. Make sure all of your connections are secure and there are no sparks or shorts. If everything is in order, you can enjoy your soldered LED light strip!
10 Effective Methods How to Solder Led Light Strips
1. Use the Correct Type of Solder
There are two types of solder that can be used for LED light strips: leaded and lead-free. Lead-based solder is more likely to contain harmful chemicals, so it is important to use lead-free solder whenever possible.
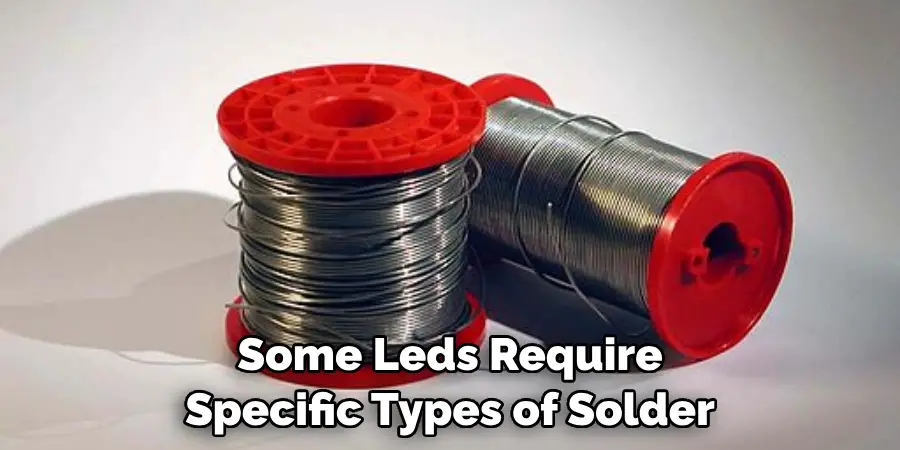
Additionally, some LEDs require specific types of solder, such as silver-bearing or rosin core. Make sure to double-check the manufacturer’s instructions for your specific LED light strips before beginning.
To ensure a strong bond, the solder should be the same size or larger than the wires on the LED light strip. To apply the solder, first heat it up with a soldering iron or gun and then touch the heated solder to both wires at once.
2. Choose the Right Size of Solder
The size of the solder you use is also important. If the solder is too small, it may not be able to adhere properly to the LED light strip. On the other hand, if the solder is too large, it may be difficult to work with and could cause damage to the LED light strip.
The best type of solder for LED light strips is a rosin-core solder with a diameter of at least 0.8mm and no more than 1.2mm. This type of solder will help ensure a strong and lasting bond between the LED light strip and the other components. Although other types of solder can be used, they may not provide the same level of durability.
3. Prepare the Surface
Before soldering, it is important to prepare the surface of the LED light strip. This can be done by using a soldering iron to tin the surface, which will help the solder to adhere more easily. If necessary, use a steel brush or sandpaper to remove any oxidation from the surface.
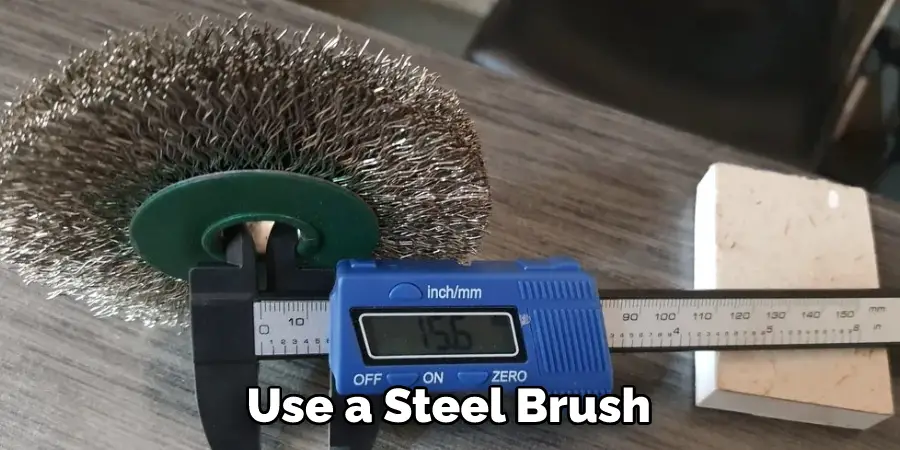
Make sure that no dirt or dust remains on the light strip before soldering, as this can cause the solder to not adhere correctly. If necessary, use a non-corrosive flux paste to give the surface an extra boost.
To prevent accidental contact with the light strip, use a pair of tweezers or needle-nose pliers to position the wires. However, if the connection is going to be permanent, it is better to use a soldering iron to directly attach the wires.
4. Apply Heat Properly
When applying heat to the LED light strip, it is important to do so evenly. Applying too much heat to one area can damage the LED light strip or cause it to become deformed. It also helps to use a soldering iron with an adjustable tip so you can easily adjust the heat and apply it evenly.
While you may be able to solder LED light strips with a soldering iron, it is best to use a hot air gun for the most even results. This will also help you avoid burning the LED light strip.
When soldering, try to keep the heat on for only a few seconds at a time and move quickly between soldering points. If you keep the heat on for too long, it can cause the LED light strip to overheat and get damaged.
5. Use Flux
Flux is a substance that helps to clean the surface of metals and allows the solder to flow more easily. When soldering LED light strips, it is important to use a flux-core solder in order to ensure that the joint is properly cleaned and soldered.
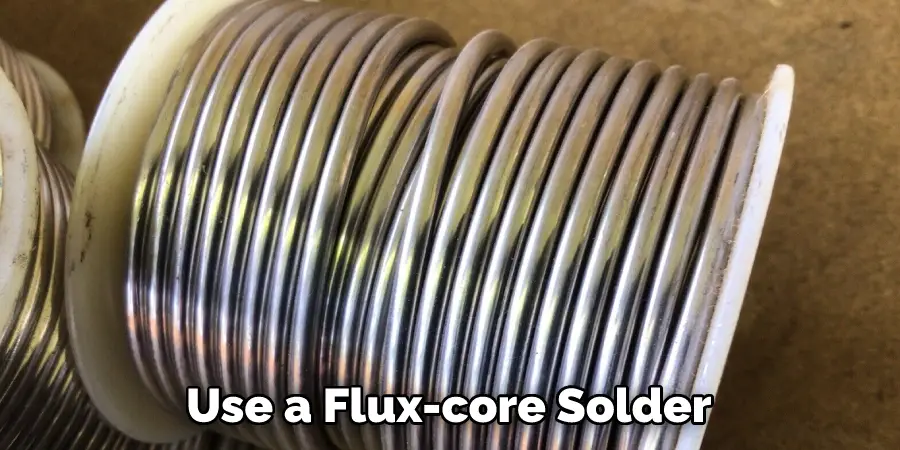
If you use rosin core solder, then you will need to apply flux to the surface of the metal before soldering. This helps to remove any impurities or oxidation on the surface of the metal, which will help ensure that the solder flows properly and securely.
To apply flux, simply dip a cotton swab into the flux and then rub it onto the area that needs to be soldered. Wait for about ten seconds for the flux to activate, then proceed to solder. To help prevent any short circuits, it is important to make sure that the area is completely cleaned before you begin soldering.
6. Keep Joints Clean
It is important to keep joints clean when soldering in order to avoid any defects in the final product. Any dirt or debris on the joint can cause problems when trying to solder it. Make sure to use a small brush or cloth to remove any dirt or debris before beginning the soldering process.
Additionally, it is important to make sure that all of the wires are properly twisted together and connected firmly in order to create a secure joint. However, it is also important to be careful when handling the wires in order to avoid any damage.
While soldering, it is a good idea to use flux or liquid solder remover in order to clean any excess solder and keep the joint free of contaminants. Although this step may seem tedious, it is necessary in order to ensure that the LED light strip will work properly.
7. Use Rosin-Based Flux
Rosin-based flux is a type of flux that helps prevent oxidation and provides a better connection between the metals being soldered. When soldering LED light strips, it is important to use a rosin-based flux in order to get the best possible connection.
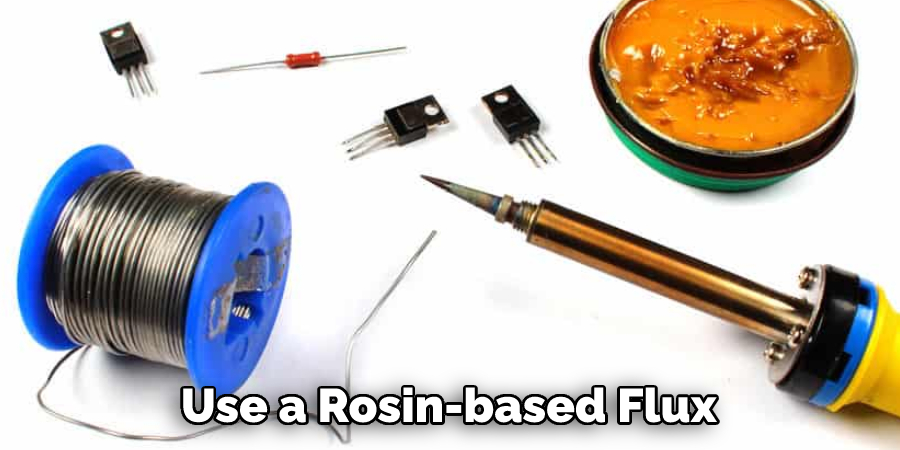
Apply a thin layer of flux across the area that is to be soldered, then proceed with the next step. To remove any excess flux residue, use a dry cloth to clean the area after soldering is complete.
If flux residue is left on the LED light strip, it can affect its performance and longevity. However, if flux residue is left on the LED light strip, it can be removed with an alcohol-based solvent.
8. Don’t Overheat The Joint
It is important not to overheat the joint when soldering, as this can damage the LED light strip or cause it to become deformed. Applying too much heat can also cause problems with adhesion and could result in a poor connection between the metals being soldered.
To avoid this, keep the soldering iron on the joint for only a few seconds at a time. Once you have achieved an even flow of solder, quickly remove the iron. This will help to ensure that the joint is properly formed and not weakened by excessive heat.
To ensure optimal performance, it is also important to use a soldering iron with the appropriate wattage for the specific project. If you are unsure, consult the manufacturer’s instructions.
9. Remove Excess Solder
Aftersolderingthejoint, it is important to remove any excess solder from the surface in order to avoid any shorts or other problems with the electrical connection. Excess solder can also make it difficult to properly insulate the joint, so it is important to remove it before proceeding further.
There are several ways to do this. The first is to use a solder wick, which is a thin copper braid that acts like a sponge and absorbs the surplus solder when heated. Another way is to use a desoldering pump, which uses suction to remove excess molten solder from the joint area.
Finally, some soldering irons are equipped with a built-in vacuum desoldering tool that can be used for this purpose. Whichever method is chosen, it is important to clean up any remaining residue from the joint before proceeding. This will help ensure a strong and reliable connection.
10 Inspect The Joint
Once the joint has been soldered, and any excess solder has been removed, it is important to inspect it for any defects or problems. This can be done using a magnifying glass or other similar devices. Look for any shorts between the wires, splices that are not completely soldered and/or cold joints (this is where the solder has failed to adhere to the metal).
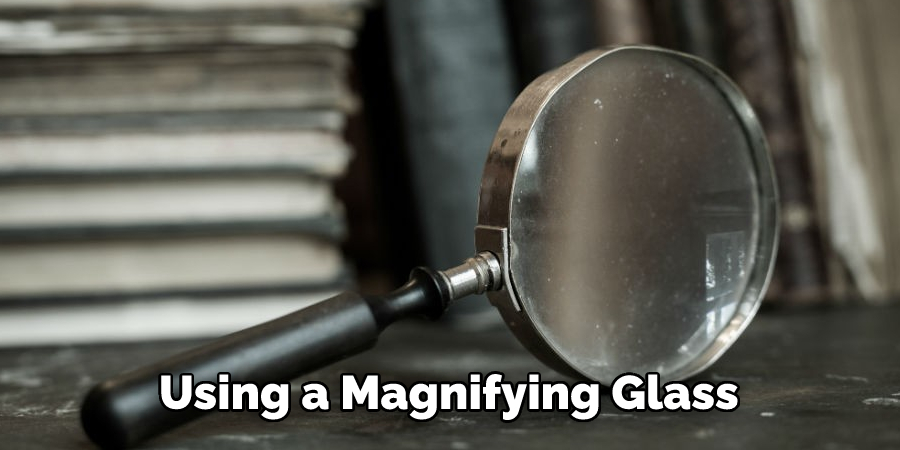
If any of these issues are present, it is best to take corrective action before continuing with the installation. Additionally, it is important to check that the LED strip is properly connected to the power source and functioning correctly.
This can be done by inspecting any visible LEDs and/or by testing with a meter. If any issues are noted during this inspection process, they should be addressed before continuing with the installation of the LED light strip.
Things to Consider When Soldering LED Light Strip
1. Soldering Iron:
Before you start, make sure that you have the right soldering iron for the job. If you are using a pre-made LED light strip, you should purchase a soldering iron with adjustable temperature settings. This will help to ensure that the solder melts properly and doesn’t damage the delicate components of the LED strip.
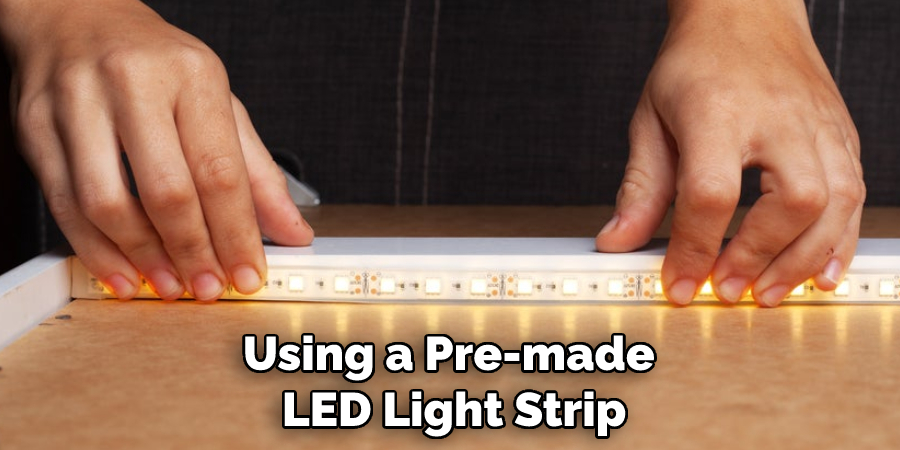
2. Solder:
It is also important to use the correct type of solder for your project. The most common solders are made from tin, lead, or silver alloys. Each type has its own properties that can affect how well it holds a connection and how long it will last. Research the types of solder available to you and choose the one that best meets your needs.
3. Heat Shrink:
Always be sure to use heat shrink tubing when soldering LED light strips together or around any other components like wires or switches. This will help protect both the connections and the components from damage caused by overheating during soldering as well as dust, dirt or moisture accumulation over time.
Conclusion
By following the above steps, LED light strips can be easily and safely soldered to bring life to any project. Soldering successfully requires care and determination, so stay focused while you are carrying out the procedure given in this post.
Once you have completed the procedure and your LED lights are successfully soldered in place, you will be able to take pride in your accomplishment! Now that you know how to solder LED light strips, go ahead and try it yourself! You may just find that soldering is a fun DIY hobby that is perfect for all sorts of projects. So what are you waiting for? Put your soldering skills to use with How To Solder Led Light Strip!